Super Capacitor Manufacturing Process
Xuansn pursues excellent engineering precision and quality standards to ensure that each supercapacitor reaches the highest level in terms of performance and reliability. Xuansn’s super capacitor manufacturing process is well thought out and strictly controlled from material selection to final assembly to ensure users receive a superior energy storage and release experience.
Quality control is a critical aspect of the manufacturing process. Xuansn is committed to monitoring various performance indicators of capacitors through strict testing processes, including capacitance value, internal resistance, cycle life, etc. Only after passing strict quality inspection procedures can products meet the high standards of the Xuansn brand, ensuring that users obtain reliable and efficient energy storage solutions in practical applications.
Through unremitting pursuit of manufacturing technology and continuous innovation, Xuansn supercapacitors have become an ideal choice for energy storage needs in various fields with their excellent performance and reliability.
Manufacturing process of wound supercapacitors
A slurry of coating material is made by mixing activated carbon, solvents and other materials.
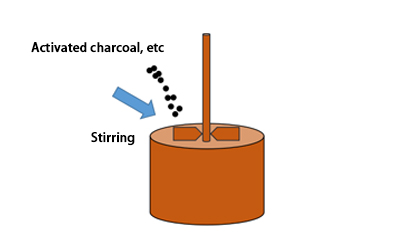
The activated carbon electrode is made by coating the activated carbon material on the aluminum foil.
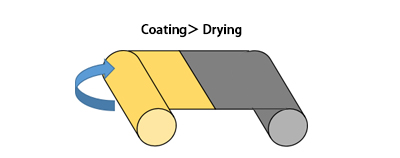
A slurry of coating material is made by mixing activated carbon, solvents and other materials.
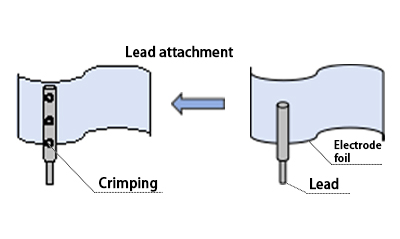
A slurry of coating material is made by mixing activated carbon, solvents and other materials.
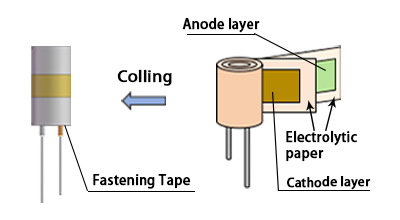
A slurry of coating material is made by mixing activated carbon, solvents and other materials.
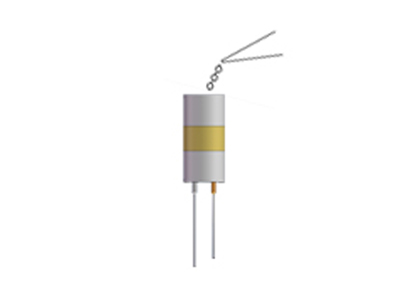
After wetting, place the rubber seal on the lead and insert the element into the housing.
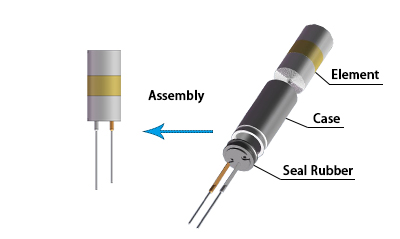
Heat shrink the sleeve printed with rated voltage, capacity, characteristics, etc. onto the capacitor.
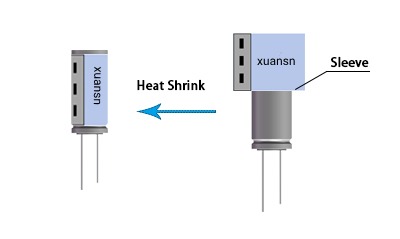
100% of units undergo electrical testing and visual inspection for troubleshooting.
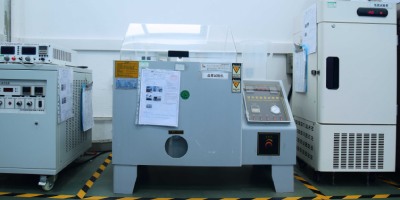
Heat shrink the sleeve printed with rated voltage, capacity, characteristics, etc. onto the capacitor.
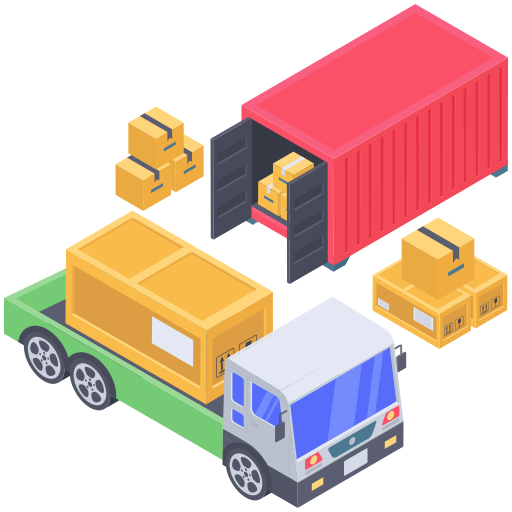
Coin Super Capacitor Manufacturing Process
Select suitable electrode materials, typically activated carbon, carbon nanotubes, etc., for the preparation of the electrode sheet.Use methods such as chemical deposition or electrochemical deposition to ensure an even distribution of electrode materials on the sheet.
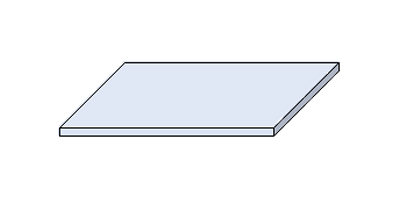
Utilize mechanical or laser equipment to create holes in the electrode sheet. The design of these holes aims to increase the surface area of the electrode, enhancing the performance of the supercapacitor.
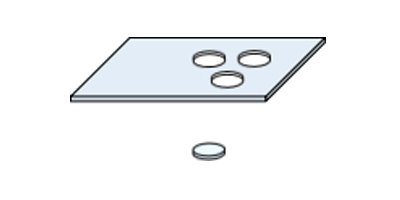
Perform adhesion treatment to ensure the stability and adhesiveness of the electrode sheet. This may involve coating the surface of the electrode sheet with an adhesive to improve its attachment to other components.
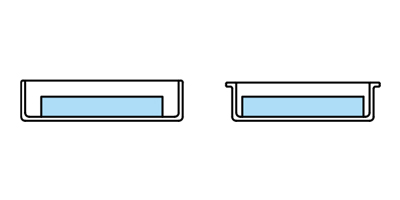
Introduce an appropriate electrolyte, typically a liquid electrolyte, into the supercapacitor to form a charge storage layer and facilitate charge conduction between positive and negative electrodes.
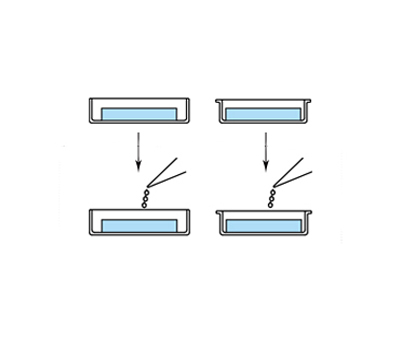
Assemble the electrode sheet and electrolyte layer according to the design and seal them together, ensuring the encapsulation of the internal environment of the supercapacitor.
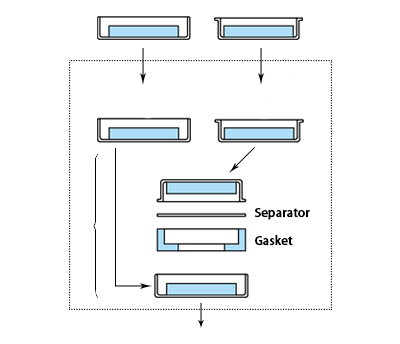
Implement layered processing, stacking the assembled capacitor layers to enhance energy density and performance.
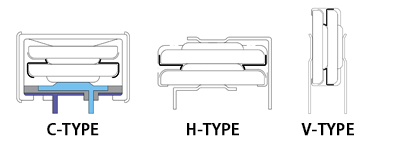
100% of units undergo electrical testing and visual inspection for troubleshooting.
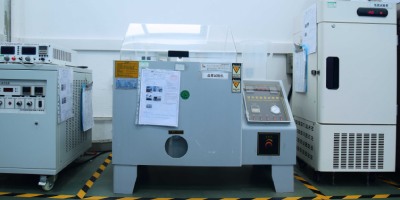
Heat shrink the sleeve printed with rated voltage, capacity, characteristics, etc. onto the capacitor.
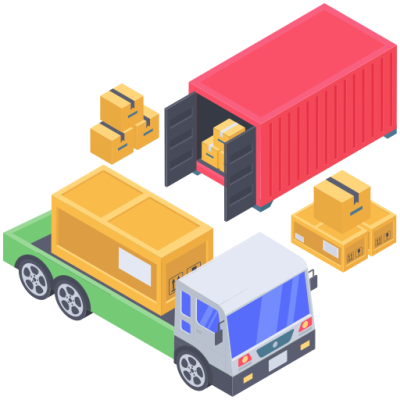